Revenu
Caractéristiques Mécaniques
Au cours du revenu, les changements dans la structure micrographique entraînent une évolution des caractéristiques mécaniques du métal.
La connaissance de ces évolutions permettra de choisir, dans chaque cas, le type de revenu à effectuer afin d’obtenir les caractéristiques mécaniques désirées.
Les deux facteurs qui influent le plus sur la structure micrographique, et donc sur les caractéristiques mécaniques, sont la température, et le temps de maintien à cette température.
Le choix de la température de revenu dépend des caractéristiques mécaniques désirées. Le revenu permet de réaliser un compromis entre la résistance mécanique et la résistance aux chocs (résilience).
Aciers non ou peu alliés
Au cours du 1° stade du revenu, on assiste à une baisse très faible de la résistance à la traction.
Par contre la limite d’élasticité Re augmente et la résilience prend une valeur convenable.
Cela est dû à la relaxation des contraintes propres existant au niveau de la maille, engendrées par la présence des atomes de carbone intersticiels.
– Lorsque la température revenu augmente, la résistance décroît régulièrement.
– La résilience décroît avant de remonter fortement pour des températures supérieures à 450/500°C.
Ceci explique que l’on pratique en général :
– Des revenus à basse température autour de 180-200°C.
– Des revenus au dessus de 450-500°C.
Plus le pourcentage de carbone est élevé et plus la dureté est grande après la trempe, la baisse de dureté au revenu sera d’autant plus importante.
Aciers fortement alliés
Pour ces aciers, la dureté est souvent la seule caractéristique représentée, car les valeurs obtenues en traction et en résilience ne sont pas très représentatives de l’aptitude à l’emploi.
Aux températures voisines de 500°C, il existe un pic de durcissement dit « secondaire », qui vient se superposer à l’adoucissement progressif de la martensite.
De ce fait, il est possible d’obtenir une dureté importante pour des températures de revenu élevées. Cette situation particulière est largement utilisée :
– Dans le travail à chaud pour résister à l’adoucissement (outillage de forge, de fonderie Aluminium…)
– Pour appliquer des traitements superficiels ultérieurs, tels que les nitrurations ou les dépôts PVD.
Remarque :
L’intensité des pics de durcissement est liée à la quantité de carbures précipitée. Celle-ci est fonction de la quantité de carbures mise en solution, donc de la température d’austénitisation.
L’exemple ci-dessous correspond à un acier de type X160CDV12 après sous austénitisation et sur-austénitisation.
Rappelons qu’avec ces aciers, il est nécessaire de réaliser 2 ou 3 revenus successifs pour déstabiliser l’austénite résiduelle, et obtenir une structure homogène et stable.
Par ailleurs il n’est pas rare que la dureté après revenu soit supérieure à la dureté après trempe.
Dureté des aciers alliés
Aciers alliés avec éléments non carburigènes
Aciers alliés avec éléments carburigènes
Comparaison
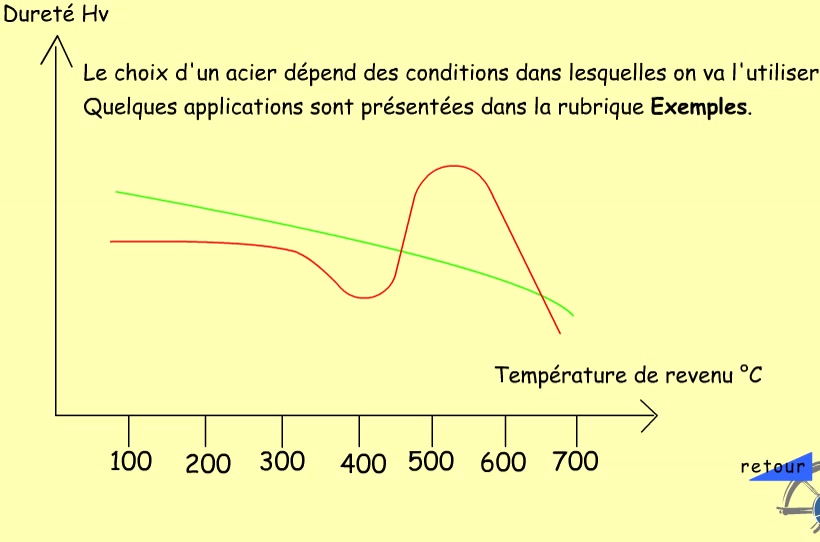
Fragilité au revenu
Le métal devient fragile dans certains domaines de température de revenu :
Revenu entre 300 et 400°C
La formation de cémentite en plaquettes est une cause de fragilité. Il vaut mieux une cémentite sous forme de sphères.
Maladie de Krupp
Elle apparaît entre 500 et 350°C au cours du refroidissement lent après revenu. Elle se manifeste surtout pour les aciers non alliés, ou peu alliés au manganèse contenant les impuretés : phosphore, étain, arsenic. Ces éléments migrent vers les joints de grain.
Conséquence
L’acier se fragilise (fragilité inter-granulaire), ce qui se manifeste par une chute importante de la résistance aux chocs.
Remèdes et Précautions générales
Les deux premières causes de fragilité sont inévitables car elles correspondent à des transformations de phase. Par contre il existe plusieurs moyens pour remédier à la maladie de Krupp :
1 – Il faut éviter de faire un revenu entre 350 et 500°C.
2 – Pour les températures supérieures, le refroidissement devra être rapide pour éviter la ségrégation des impuretés. Il s’agit alors « d’arrêt de revenu à l’huile ».
3 – Eviter les éléments fragilisants. En conséquence, préférer les aciers dont la qualité d’élaboration est reconnue.
4 – Utiliser des aciers contenant au minimum 0.15% de molybdène, ou encore plus alliés.
Pour les aciers non ou peu alliés
Lorsque la température est suffisamment élevée (supérieure à 150°C), l’allure des courbes en fonction du temps est la suivante :
La plus grande variation de la dureté a lieu dès les premiers instants du revenu. Il est donc inutile de prolonger le revenu car ses effets sont ensuite négligeables.
Le temps de maintien joue peu sur le niveau de dureté, sauf pour les revenus de détente (basse température).
Pour les aciers fortement alliés
La présence d’éléments carburigènes permet une précipitation de carbures alliés autour de 500°C.
Dans ce cas, le temps de maintien joue un rôle plus important car le phénomène progresse avec le temps.
A titre indicatif, on applique une heure pour une section circulaire de 25 mm de diamètre lorsque la surface arrive à température et une heure de plus par 25 mm supplémentaire.
Un maintien de 5 à 10 heures fait perdre de l’ordre de 2 à 4 points HRC selon les nuances.
Nous verrons également des exemples de revenus sur des nuances caractéristiques.
Acier faiblement allié : 90MnCrV8
Influence du Chrome : X38CrMoV5
Influence des éléments carburigènes : X160CrMoV12
Il s’agit d’un acier faiblement allié. Son domaine d’application se situe aux duretés élevées, donc aux températures de revenu de l’ordre de 180/200°C.
Composition en %
Carbone : 0.90
Manganèse : 2.00
Chrome : 0.40
Vanadium : 0.10
Traitement
Trempe : Chauffage à 800°C
Trempe à l’huile
Revenu : à partir de 150°C
Propriétés
Acier de bonne dureté, tenace, résistant bien aux chocs répétés.
Applications
Acier pour travail à froid utilisé pour :
Outils de découpage, matrices, calibres.
Il s’agit d’un acier fortement allié.
Composition en %
Carbone : 1.65
Molybdène : 0.50
Tungstène : 0.50
Chrome : 12
Vanadium : 0.25
Traitement
Trempe : Préchauffage à 750°C + Austénitisation à 1000°C ou 1040°C
Refroidissement sous gaz ou à l’huile (selon section)
Revenu : Selon l’application :
Un revenu vers 200°C, après austénitisation à environ 1000°C
Ou deux revenus vers 500°C, après austénitisation à environ 1040°C.
Propriétés
Acier résistant à l’usure, bonne tenue à la coupe.
Aptes aux durcissements superficiels de type nitruration ou PVD si revenu supérieur à 500°C.
Applications
Outillage de découpage, lames de cisaille et de broyeur.
Matrice et poinçon d’emboutissage, moules matières plastiques.