Notions de base
Introduction
D’une façon générale, il faut considérer que les essais mécaniques sont destructifs et nécessitent la réalisation d’éprouvettes :
– Soit issues de la pièce
– Soit issues d’un demi-produit représentant la pièce à tester.
L’essai de traction consiste à soumettre une éprouvette du matériau à étudier à une traction et à mesurer les contraintes mises en jeu et l’allongement correspondant.
Une machine de traction est constituée d’un bâti rigide qui comprend une traverse fixe à laquelle est fixée l’une des têtes de l’éprouvette par l’intermédiaire des mors. L’autre extrémité de l’éprouvette est fixée à une traverse mobile.
Le mouvement de la traverse mobile est assuré soit par une commande hydraulique (vérins), soit par des vis sans fin. La charge imposée à l’éprouvette est mesurée par un dynamomètre, et l’allongement par un extensomètre, ce qui permet d’obtenir un enregistrement de la courbe de traction, F = f(Δl), caractéristique du comportement mécanique de l’échantillon.
L’exploitation de la courbe de traction permet d’obtenir les caractéristiques mécaniques suivantes :
– La limite d’élasticité,
– La résistance à la traction,
– L’allongement à la rupture,
– Le coefficient de striction
Cet essai n’est pas toujours réalisable :
– Soit parce que la pièce est trop petite pour prélever une éprouvette
– Soit parce qu’on ne peut pas la détruire (pièce unitaire).
De ce fait, il est possible de se faire une idée de la Résistance à la traction par équivalence avec un essai de dureté (HV ou HB).
Toutefois, il n’existe pas de correspondance avec la limite élastique, valeur très importante en mécanique.
Limite d’élasticité
Elle peut être notée Re, σe ou E.
La limite d’élasticité correspond à la contrainte à partir de laquelle le comportement du matériau s’écarte de la loi de Hooke, c’est à dire au moment où apparaît la première déformation plastique irréversible.
En pratique, ce passage est très difficile à apprécier car il se fait de façon progressive. On lève toute ambiguïté en définissant une limite d’élasticité conventionnelle à 0,2% notée Rp0.2 qui est la résistance correspondant à un allongement de 0,2%.
Résistance à la traction
(ou encore résistance à la rupture ou charge à la rupture en traction).
Elle est notée Rm, σr ou R.
Elle est définie comme étant la contrainte maximale atteinte durant l’essai de traction.
Dans le cas des matériaux fragiles, la limite d’élasticité et la résistance à la traction sont confondues puisque ceux-ci n’ont pas de domaine de déformation plastique.
Allongement à la rupture
Il est noté A%.
Il peut être lu directement sur la courbe de traction ou mesuré sur l’éprouvette rompue.
Si Lu est la distance entre repères après rupture (les surfaces de rupture étant mises en contact), l’allongement à la rupture A est donnée par la relation suivante :
A%=(Lu-Lo)x100/Lo
où Lo est la longueur initiale de l’éprouvette.
L’allongement à la rupture est une mesure de la ductilité ; il est donc nul pour les matériaux fragiles.
Striction à la rupture
Elle est notée Z%.
La striction est la variation de la section à l’endroit où la rupture s’est produite ; elle est donnée par la relation suivante :
Z%=(Sf-So)x100/So
où :
So est la section initiale de l’Èprouvette, et
Sf la section de la surface de rupture.
Comme l’allongement à la rupture, la striction donne une indication sur la ductilité du matériau.
A la rigidité, à la résistance à la traction et à la ductilité, il faut ajouter une autre propriété fondamentale des matériaux, la résilience. On mesure cette caractéristiques par l’énergie requise pour entrainer la rupture par choc d’une éprouvette normalisée.
La résilience des matériaux dépend non seulement de leur ductilité caractérisée par A% mais également de leur limite d’élasticité et de leur résistance à la traction Rm.
Notons qu’en général, la résilience évolue en sens inverse de la dureté.
Au cours de cet essai, on rompt une éprouvette entaillée mécaniquement (dans le but de fragiliser l’éprouvette) à l’aide d’un mouton pendule CHARPY de masse m, qu’on laisse tomber d’une hauteur h0. On détermine l’énergie absorbée par la rupture de l’éprouvette, soit :
W = m x g x ( h0 – h )
où :
g est l’accélération gravitationnelle
W est l’énergie absorbée.
La résilience est étroitement liée à la température et au sens de prélèvement des éprouvettes.
– Les déformations plastiques – Les déformations élastiques – Le frottement entre le pénétrateur et le matériau – La géométrie du pénétrateur – Les propriétés mécaniques du pénétrateur – La charge appliquée sur le pénétrateur
Le tableau ci-dessous résume les caractéristiques des principales méthodes de mesure de dureté : la dureté Brinell (HB), Vickers (HV), Rockwell (HR).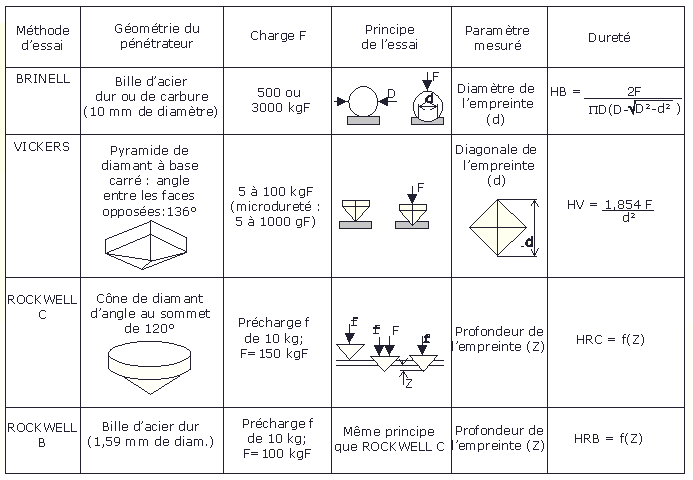
Brinell
Animation
Vickers
Comme dans l’essai Brinell, on mesure les dimensions de l’empreinte laissée par le pénétrateur. Ce pénétrateur est une pyramide à base carrée, en diamant, d’angle au sommet de 136° (cet angle a été choisi pour avoir la correspondance Brinell-Vickers). L’empreinte laissée par le pénétrateur est donc carrée. Grâce à un microscope micrométrique lié à la machine, on mesure les deux diagonales, et l’on fait la moyenne.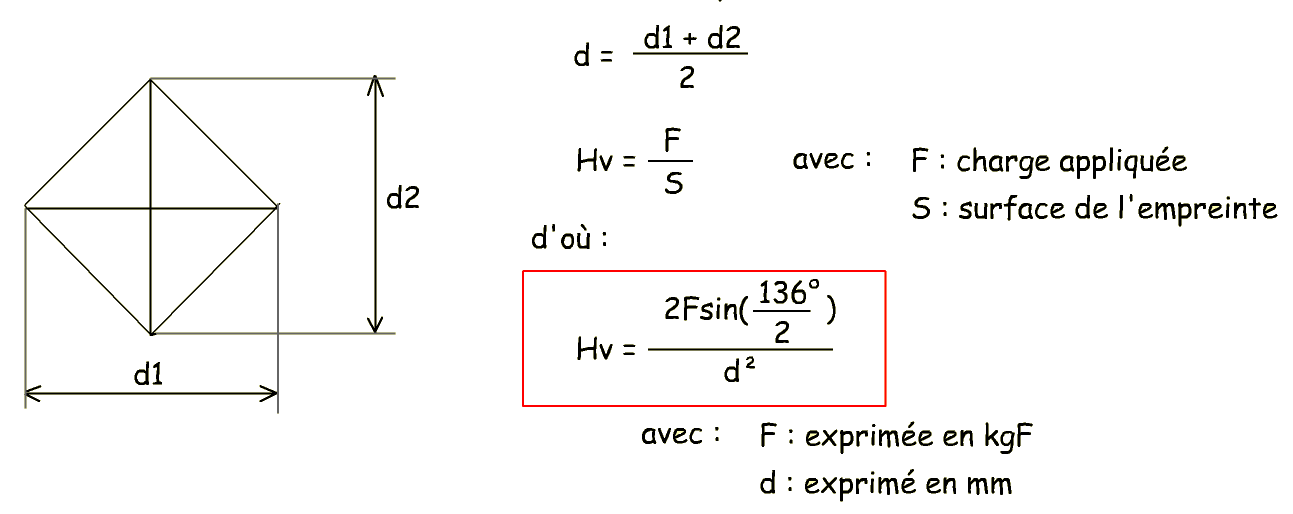
Rockwell
Alors que dans les deux essais précédents (essai Brinell et essai Vickers) on mesurait la surface de l’empreinte, l’essai Rockwell consiste à mesurer la profondeur de celle-ci. La mesure comporte trois étapes :1. Application de la précharge P0 = 10 kg 2. Application de la surcharge P1 qui permet d’atteindre la charge d’essai 3. Retour à la précharge et lecture de l’indicateur d’enfoncement. Cet indicateur est un comparateur permettant des lectures au micron près.
La méthode consiste donc à mesurer l’accroissement rémanent e de la profondeur de pénétration après supression de la surcharge. Ensuite, on lit directement l’indice de dureté correspondant à la valeur e. Cette mesure de dureté est exprimée en unités Rockwell, correspondant chacune à 0.002 mm d’enfoncement. Principe de la mesure :Animation
L’essai de compression consiste à soumettre une éprouvette de forme cylindrique à deux forces axiales opposées, en la plaçant entre les plateaux d’une presse.
La réalisation de cet essai comporte deux difficultés qui limitent l’emploi et l’exploitation des résultats expérimentaux.
Si l’éprouvette est trop haute par rapport à son diamètre, il y a risque d’apparition d’une instabilité élastique, le flambage. Pour éviter ce problème, le rapport h/d est maintenu inférieur à 3.
La seconde difficulté provient du frottement qui s’exerce entre les faces d’appui de l’éprouvette et les plateaux de la machine d’essai. Ce frottement s’oppose à l’augmentation du diamètre de l’éprouvette quand sa hauteur diminue. Il en résulte des déformations hétérogènes qui confèrent à l’éprouvette une forme de tonneau.
Les essais de compression sont surtout utilisés pour déterminer la contrainte de rupture des matériaux fragiles, qui, du fait des défauts qu’ils comportent, résistent mal à la traction.
Ils sont globalement peu utilisés sur les aciers.